在齒輪加工中,齒輪硬化層太淺或太深,導致原因有以下幾點:
1發(fā)生原因
齒輪加工的齒輪材料太硬或太高,碳含量太高或太低
對策:
1)根據(jù)齒輪尺寸和技術(shù)要求選擇淬火鋼。
2)齒輪的碳含量必須符合gb / t 699-1999和gb / t 3077-1999的規(guī)定,并且其組件偏差必須符合gb / t 222-2006的規(guī)定。
2.原因產(chǎn)生
電流過細或過深,選擇錯誤的感應加熱頻率,過高或過低,在這種情況下都沒有選擇合理的比功率和加熱時間,固化層的深度不符合技術(shù)要求。要求,直接影響加熱層的深度。
對策:
(1)根據(jù)淬火層的深度合理選擇感應加熱頻率從現(xiàn)在開始將逐步介紹各種淬火層的深度與電流頻率之間的關(guān)系。
(2)當固化層的深度大于在常規(guī)機器的頻率下可能的電流穿透深度時,可以在表面不過熱的條件下使用。
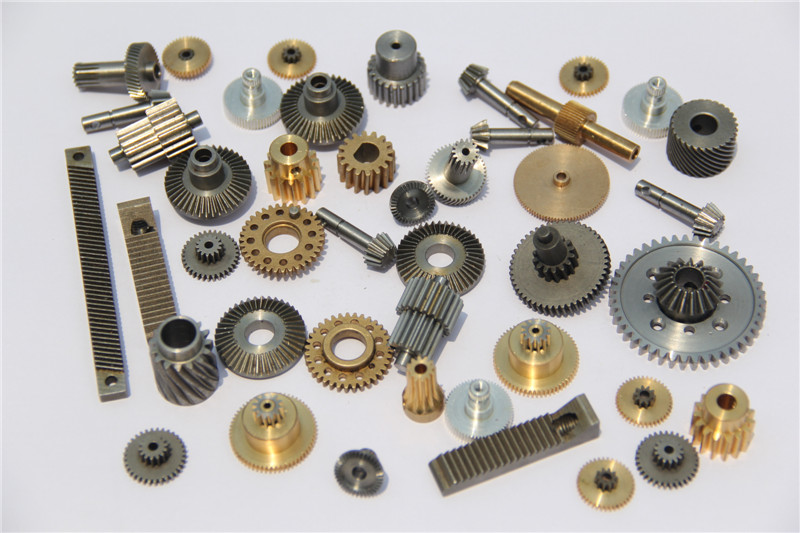
通過以下方法獲得更深的硬化層
1)降低比功率并延長加熱時間。連續(xù)加熱淬火會降低傳感器和齒輪的相對運動速度
2)適當打開齒輪和感應器之間的間隙以延長加熱時間,或使用間歇加熱方法延長同時加熱期間的導熱時間。
3)在感應加熱之前,將齒輪預熱到傳感器
4)對于連續(xù)加熱,請使用雙繞組或多繞組傳感器
5)如果齒輪尺寸較大且設備功率不足,請進行連續(xù)連續(xù)淬火,以盡可能減小傳感器內(nèi)部的加熱表面積,以增加比功率,并同時進行預熱。
3.原因產(chǎn)生
如果感應加熱時間太短或太長,齒輪表面的加熱溫度和加熱深度將大幅度發(fā)揮作用,并確定硬化層的深度。
對策:有必要根據(jù)齒輪淬火層的深度合理設定感應加熱時間。
4.原因產(chǎn)生
單位功率太高或太低,這會影響加熱時間的長短,表面加熱溫度和加熱速率以及材料的奧氏體化溫度。
對策:有必要根據(jù)齒輪淬火層的深度合理選擇單位功率。
5.原因是天生的
如果傳感器和齒輪之間的間隙太小或太大,則加熱深度將不同,而硬化層的深度將明顯不同。
6.原因是天生的
齒輪(或傳感器)在連續(xù)淬火過程中移動得太快或太慢
作為對策,當采用齒輪連續(xù)淬火方法時??,可以通過實驗確定合適的運動速度
7由于
淬火冷卻工藝不當,例如淬火冷卻介質(zhì)溫度,壓力和成分選擇不當
對策:改善淬火冷卻過程,提高冷卻速度,并采用預熱方法。
由硬化層的不平整引起
1發(fā)生原因
在同時加熱的情況下,齒輪處于偏心位置
對策:在同時加熱的情況下,將齒輪位置設置為正常位置。
2.原因產(chǎn)生
傳感器噴泉孔不均勻
對策:在設計和制造傳感器時,均勻地排列噴氣孔,以使淬火部分均勻冷卻。
3.原因產(chǎn)生
淬火車床的頂部和底部有不同的心
對策:淬火機床的頂部和底部的同心度<0.05 mm。
4.原因產(chǎn)生
齒輪材料的內(nèi)部結(jié)構(gòu)不良(當出現(xiàn)嚴重的帶狀結(jié)構(gòu)或網(wǎng)狀碳化物時)
對策:保證原材料質(zhì)量并檢查高倍率結(jié)構(gòu)。在感應淬火之前,應先對齒輪進行點火或回火
硬化層的深度變化超出要求的范圍
1發(fā)生原因
齒輪材料元素。除了改變c和mn的量外,其他合金元素,特別是諸如mo和cr之類的元素也會影響材料的淬火,并且加熱層的深度在切削刀具的檢查中是相似的,但是深度如果該值發(fā)生顯著變化,則可能是一個重要因素。
對策:保證原料質(zhì)量,檢查影響淬透性的化學元素成分,主要化學成分偏差必須符合gb / t222-1999規(guī)定。
2.原因產(chǎn)生
淬火冷卻介質(zhì)的壓力,流速,液體溫度和濃度會影響淬火層的深度,因此應進行檢查。
對策:加強淬火和冷卻規(guī)格。檢查淬火冷卻介質(zhì)的壓力,流量,液體溫度和濃度是否符合要求
3.原因感應加熱規(guī)格有很大變化,連續(xù)淬火齒輪架的移動速度也有變化。
對策:檢查感應加熱規(guī)格的變化是否很大,并且連續(xù)淬火齒輪使滑架的移動速度穩(wěn)定。